-
バンド乾燥機では、リボン状の石けん素地に温風を吹き付けて乾燥させます。左右にバンドを動かすことでリボン状の石けん素地を行き来させ、均一に温風を吹きかけ乾燥させることで石けん素地の含水率を下げていきます。
-
バンド乾燥機を経ると、石けん素地の含水率は12%まで下がります。次に造粒機で幅10㎜~15㎜、直径5㎜のヌードル状(ソープヌードル)にします。さらに、後の工程で混合・練成しやすいチップ状にまで加工します。
-
輸送前の石けん素地を試験します。項目は遊離アルカリや揮発分、色など多岐に渡ります。試験に合格したものだけが、化粧石けん用の素地として使われます。空気圧によってチューブの中を運ばれたチップ状の石けん素地は輸送用容器(フレコンバッグ)に充填され、その後、山梨県にある富士河口湖工場に運ばれます。
-
墨田工場から運ばれたチップ状の石けん素地を、ミキサー機に入れて混合します。製品によっては精油(エッセンシャルオイル)や、植物エキスなどの保湿成分、ハーブの粉末を加えていきます。輸送中にできたチップの固まりをほぐしたり、エキス等が全体にまんべんなく行き渡るよう、時間をかけて丹念に混合します。
-
石けん素地をミキサー機からローラー機に移します。チップ状の石けん素地は、輸送の過程で外側が乾燥して硬くなり、内側がやわらかくなっています。均一にするため、ロールにかけてなめらかにし、押し出し機に移します。
-
石けん素地をきめ細かくするため、押し出し機を通る間にメッシュに通します。押し出し機では石けん素地を加温・圧縮し、専用の口金で押し出します。なめらかで割れにくい石けんにするための工程です。
-
細長い棒状に押し出された石けん素地をひとつひとつ専用の金型で型打ちします。型打ちとは成型工程のことです。見た目に美しくするだけでなく、手に持ったときに使いやすい形と大きさに整えるための作業です。
-
型打ちされた石けんをスタッフが両手で受け取り、すのこにテンポよく並べていきます。同時に、異物が混入していないか、傷や変形はないか、刻印は正しい位置にされているか、かすれていないか等をチェックします。
-
包装前に中間試験で重量等を試験します。合格するといよいよ包装です。製造番号を印字し、正しく印字されているかひとつひとつ目視確認します。包装後にも最終試験があり、合格したもののみがお客様のお手元に出荷されます。
松山油脂のモノづくり / 機械練り製法
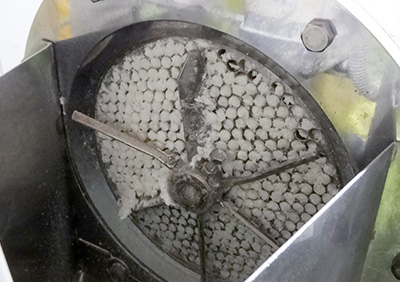
最後はひとつひとつ、人の目と手で
タンクから、純度が高まった、熱く粘性のある石けん(ニートソープ)を、冷却用の回転ドラムに滴らせます。すると、ドラムの表面で石けんが瞬時にうすく固まります。そのうすく固まった石けんを大きな熊手のような爪で自動的に掻き取ってリボン状にし、乾燥機に送ります。